ค่าดัชนี Cp และ Cpk เป็นค่าที่เราๆรู้จักกันเป็นอย่างดี ได้ถูกนำมาใช้ในการดูการกระจายของกระบวนการเทียบกับช่วงความกว้างอนุโลม (tolerance interval) นั่นคือค่า Cp ส่วนค่า Cpk ซึ่งเป็นการดูว่ากระบวนนั้นยังอยู่ภายใต้ข้อกำหนดเฉพาะหรือไม่
แต่ยังมีอีกหนึ่งดัชนี คือ Cpm ซึ่งอาจไม่ได้เป็นที่รู้จักมากและไม่ค่อยมีการนำมาใช้บ่อยนัก ความแตกต่างของค่า Cpm กับค่าดัชนีอื่นๆ คือ ค่าความแตกต่างจากเป้าหมาย (Bias) จะถูกนำมาพิจารณาในการหาค่า Cpm ซึ่งค่าความแตกต่างระหว่างค่าเฉลี่ยของกระบวนการและค่าเป้าหมายจะเรียกว่า Bias
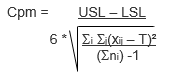
เมื่อ USL คือ ค่าพิกัดเขตกำหนดเฉพาะด้านบน,LSL คือ ค่าพิกัดเขตกำหนดเฉพาะด้านล่าง,S คือ ค่าเบี่ยงเบนมาตรฐาน,T คือ ค่าเป้าหมายและให้

และ
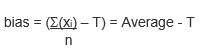
หมายเหตุ ในสูตรการหาค่า Cpm ค่า input คือ bias และค่า Bias ยิ่งมาก ค่า Cpm จะยิ่งมีค่าน้อยลง
ประเด็นเรื่องความไม่เข้ากันของการประกอบชิ้นส่วน
ทำไมเราควรใช้ค่า Cpm แทนการใช้ค่าดัชนีค่าอื่นๆ เพราะค่า Cpm เป็นค่าสัมประสิทธิ์ที่มีประสิทธิภาพในการที่ช่วยลดปัญหาเรื่องความไม่เข้ากันในการประกอบชิ้นส่วน (component mismatch)
ในหลายๆครั้งของการผลิตจะต้องมีการประกอบชิ้นส่วนต่างๆเพื่อให้เป็นผลิตภัณฑ์ และในบางครั้งแม้ว่าชิ้นส่วนที่ผลิตมาจากกระบวนการที่มีค่า Cpk ดีมาก แต่เมื่อระบบการผลิตทำการประกอบชิ้นส่วนที่มาจากการผลิตนั้นๆ กลับทำให้ได้ผลิตภัณฑ์ที่ไม่ตรงตามข้อกำหนดเฉพาะ
ทำไมถึงเป็นเช่นนี้ได้ สมมติว่ามีชิ้นส่วน 2 ชิ้นมากประกอบกัน โดยออกแบบให้มีการสวมประกอบกัน ตัวอย่างเช่น เพลาจะสวมประกอบลงในรูเพลา โดยเพลาที่สวมลงนั้นจะมีขนาดเล็กว่ารูเพลาเล็กน้อยเพื่อให้ยังสามารถเคลื่อนที่ได้เล็กน้อย

ในการวิเคราะห์ความสามารถต่อไปนี้ ค่า Ppk นั้นสะท้อนว่ากระบวนการผลิตเพลาและรูเพลาดีมากทั้งสองอย่าง (ค่าดัชนีประมาณ 2 ทั้งสองกระบวนการ) แต่ค่า Cpm กลับมีค่าต่ำทั้งคู่ (ประมาณ 1.2) เนื่องมาจากมีการเบี่ยงเบนไปจากค่าเป้าหมายอย่างมีนัยสำคัญ จากกราฟในรูปด้านล่างแสดงให้เห็นว่า เพลา มีขนาดใหญ่กว่าที่ควรจะเป็น ส่วนรูเพลามีค่าเล็กกว่าที่ควรจะเป็น (ค่าเฉลี่ยน้อยกว่าค่าเป้าหมาย) ผลที่ตามมาคือ ชิ้นส่วนทั้งสองชิ้นนี้มักสวมประกอบกันไม่ได้ บางครั้งการใส่เพลาลงรูเพลาเป็นไปด้วยความลำบาก เพราะมีค่า bias ที่เพิ่มขึ้น ทำให้เกิดความไม่เข้ากัน (mismatch)

การทำให้ค่า bias มีค่าเล็กที่สุดเท่าที่จะเป็นไปได้ ในระบบที่ซับซ้อนที่ต้องมีประกอบกันของชิ้นส่วนหรือพารามิเตอร์ต่างๆด้วยกัน ไม่ควรจะมีการแยกพิจารณา ในผลิตภัณฑ์ที่มีความซับซ้อนประกอบจากชิ้นส่วนจำนวนมากและมาจากหลายแหล่งผลิต การดูแลระบบย่อยต่างของชิ้นส่วนทั้งหมดจะถูกนำมาพิจารณาร่วมกันแทนที่จะแยกกันพิจารณาคุณภาพของแต่ละชิ้นเดี่ยวๆ
ในบทความนี้ แสดงให้เห็นว่า ค่า Cpm นั้นเป็นค่าดัชนีที่มีประสิทธิภาพที่ดีกว่าค่าดัชนีตัวอื่นๆ
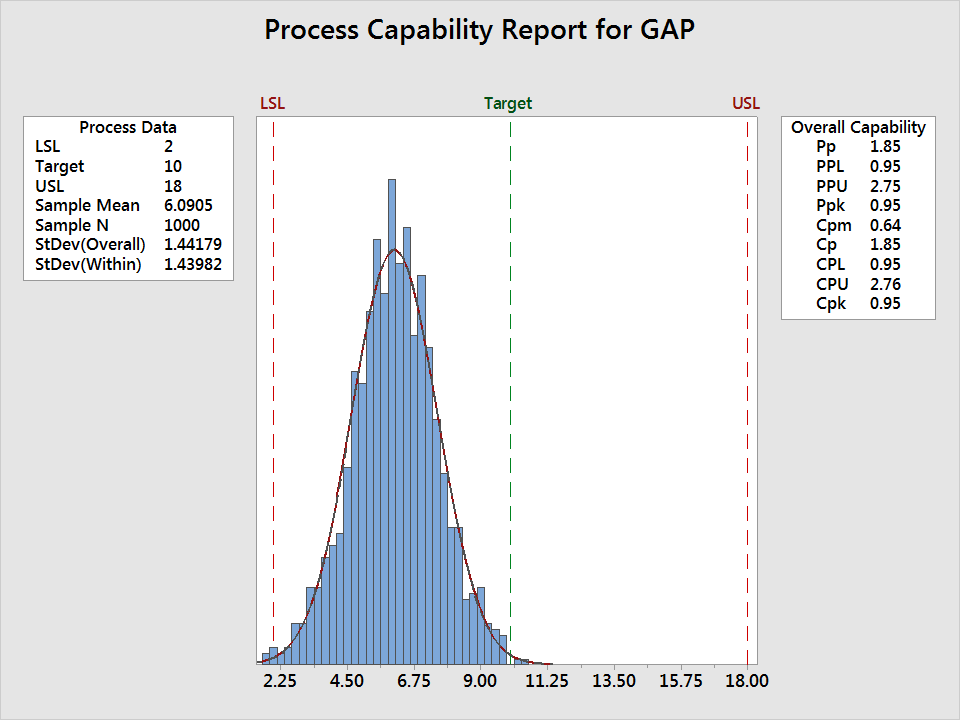
จากกราฟในรูปบนนี้แสดงให้เห็น ค่าความต่างระหว่างขนาดเพลาและรูปเพลา ค่าเป้าหมายของช่องว่างระหว่างเพลาและรูเพลา คือ 10 (ค่าเป้าหมาย) ค่า Ppk (0.95) ที่ได้แสดงว่าเป็นกระบวนการที่ไม่ดี ซึ่งจะทำให้เกิดการสวมประกอบที่ไม่เป็นตามข้อกำหนดเฉพาะ จากชิ้นส่วนเดี่ยวๆ ค่า Bias ของแต่ละชิ้นส่วนไม่ได้มีค่ามาก แต่เมื่อนำชิ้นส่วนมาประกอบกัน ค่า bias ของชิ้นส่วนที่ประกอบกันแล้วมีค่ามากขึ้น
ถ้าค่า bias ของเพลาและรูเพลาเป็นบวกเหมือนกัน นั้นอาจทำให้ชิ้นส่วนที่มาประกอบกันนั้นอาจจะไม่เกิดปัญหา เพราะค่า bias จะทำการหักล้างกัน แต่ในหลายๆกรณี ค่า bias ของชิ้นส่วนจะทำให้ผลสุดท้ายมีค่ามากขึ้น จากตัวอย่างนี้เป็นเพียงชิ้นส่วนประกอบกัน 2 ชิ้น แต่ในความเป็นจริงระบบการผลิตอาจจะเกิดจากการประกอบชิ้นส่วนจำนวนมากกว่านี้ยิ่งทำให้มีความซับซ้อนมากขึ้น
การใช้ Cpm กับกรณีค่าเป้าหมายที่ไม่ได้อยู่กึ่งกลาง
ประโยชน์อีกข้อหนึ่งของ Cpm คือ ถ้าค่าเป้าหมายไม่ได้อยู่กึ่งกลางระหว่างข้อกำหนดเฉพาะ จะต้องมีการตรวจติดตามดูค่าเฉลี่ยว่าตรงกับค่าเป้าหมายอย่างใกล้ชิด ค่า Cpm จะมีความเกี่ยวพันโดยตรงมากกว่า ค่า Ppk

ค่าดัชนีความสามารถ Cpm มาจากแนวคิดของ เส้นโค้งความเสียหาย (Loss Curve) ของ Taguchi (ปราชญ์ด้านคุณภาพชาวญี่ปุ่น) จากแนวคิดที่ว่าคือ เมื่อใดที่ค่าเฉลี่ยของกระบวนการเริ่มเบี่ยงเบนจากค่าเป้าหมายจะเริ่มมีความสูญเสีย/เสียหาย (loss) เกิดขึ้น และคุณภาพที่ได้จะเริ่มแย่ลง ดังนั้นการที่ทำให้อยู่ภายใต้ข้อกำหนดเฉพาะเท่านั้นไม่เพียงพอ แนวคิดเรื่องความสูญเสียของลูกค้าเมื่อชิ้นส่วนนั้นไม่อยู่ในข้อกำหนดเฉพาะเท่านั้นจึงเป็นเรื่องที่ไม่ถูกต้อง ในมุมมองของลูกค้า ไม่ว่าจะผลิตภัณฑ์ที่แทบจะไม่ตรงกับข้อกำหนดเฉพาะนั้น ไม่ว่าจะดีหรือไม่ดี ลูกค้าจะมองว่าเป็นของที่ไม่ตรงกับข้อกำหนดเฉพาะ
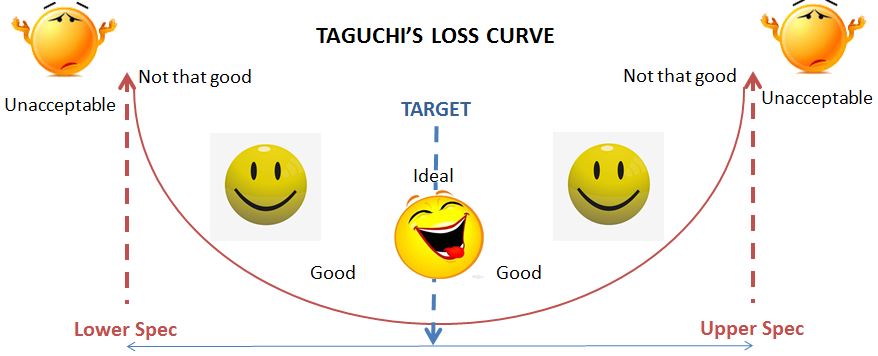
เส้นโค้งความเสียหายทางคุณภาพ (Quality loss curve )เป็นสัดส่วนที่ขึ้นกับ ค่ากำลังสองของระยะห่างจากค่าเป้าหมาย
บทสรุป
ในช่วงเริ่มต้นของการเปลี่ยนแปลงในอุตสาหกรรม เริ่มต้นจากการใช้ฝีมือแรงงานที่ทำการประกอบชิ้นส่วนกันอย่างระมัดระวัง แต่ในยุคการผลิตแบบเชิงมวล ( Mass production) เนื่องจากข้อจำกัดด้านเวลา ความซับซ้อนของผลิตภัณฑ์ และ จำนวนชิ้นส่วนย่อยที่ประกอบกันจึงทำให้ไม่สามารถใช้แรงงานฝีมือต่อไปได้
ในบทความนี้ ค่าดัชนี Cpm จะถูกนำมาใช้เพื่อหลีกเลี่ยงการไม่สามารถประกอบกันได้ของชิ้นส่วนย่อยต่างๆ ไม่เฉพาะเพียงเรื่องขนาดของชิ้นส่วนเท่านั้นแต่ค่าคุณสมบัติอื่นๆที่สะท้อนผลกระทบที่จะส่งถึงผลิตภัณฑ์สุดท้ายก็สามารถใช้ดัชนีได้
บทความต้นฉบับ : How Could You Benefit from the Cpm Capability Index?
ต้นฉบับนำมาจาก Minitab blog, แปลและเรียบเรียงโดยสุวดี นำพาเจริญ
บริหารจัดการ SCM Blog โดยชลทิชา จำรัสพร บริษัท โซลูชั่น เซ็นเตอร์ จํากัด ตัวแทน Minitab ในประเทศไทย

เพิ่มเติมเกี่ยวกับบริษัท Minitab
Minitab ช่วยให้บริษัทและองค์กรต่างๆ สามารถมองเห็นแนวโน้มของข้อมูล, แก้ปัญหาและค้นพบประเด็นสำคัญจากข้อมูลเชิงลึก โดยนำเสนอชุดโซลูชั่นที่ครอบคลุมทุกด้านและดีที่สุดสำหรับซอฟต์แวร์ในระดับเดียวกัน ที่ใช้สำหรับการวิเคราะห์ข้อมูลและการปรับปรุงกระบวนการ
ด้วยวิธีการที่เป็นเอกลักษณ์ และการนำเสนอซอฟต์แวร์และบริการแบบองค์รวม Minitab ช่วยให้องค์กรเข้าถึงกระบวนการตัดสินใจในส่วนที่ช่วยผลักดันให้เกิดความเป็นเลิศทางธุรกิจได้ดีขึ้น ความง่ายในการใช้งานที่โดดเด่นกว่าใครมีส่วนช่วยให้ Minitab สามารถทำให้การเข้าถึงข้อมูลเชิงลึกเป็นเรื่องที่ง่าย ทีมงานของ Minitab ซึ่งประกอบด้วยผู้เชี่ยวชาญทางด้านการวิเคราะห์ข้อมูลที่ได้ผ่านการอบรมมาเป็นอย่างเข้มงวด จะช่วยให้ผู้ใช้งานมั่นใจว่าจะได้รับประโยชน์สูงสุดจากการใช้งานวิเคราะห์ข้อมูลและพร้อมที่จะให้คำปรึกษาตลอดเวลาที่ใช้งานเพื่อนำไปสู่การตัดสินใจที่ดีขึ้น รวดเร็ว และแม่นยำ
เป็นเวลากว่า 50 ปีที่ Minitab ได้ช่วยองค์การต่าง ๆ เพิ่มรายได้ ควบคุมและลดต้นทุน เพิ่มคุณภาพ เสริมสร้างความพึงพอใจของลูกค้า และเพิ่มประสิทธิภาพ ธุรกิจและองค์นับหมื่นทั่วโลกใช้ Minitab Statistical Software®, Companion by Minitab®, Minitab Workspace®, Salford Predictive Modeler® and Quality Trainer® เป็นเครื่องมือช่วยในการค้นพบและปรับปรุงความบกพร่องในกระบวนการ