เบียร์เป็นสินค้ายอดนิยมไปทั่วโลก ปริมาณการบริโภคเบียร์ทั่วโลกมีอัตราเพิ่มขึ้นตลอด 28 ปีที่ผ่านมาเป็นจำนวนมากกว่า 193 พันล้านลิตร ผู้ผลิตเบียร์คราฟท์ของประเทศสหรัฐอเมริกามีอัตราการเติบโตในตลาดส่วนนี้อย่างชัดเจน โดยมีผู้ผลิตเกิดใหม่จำนวน 165 ราย และมีอัตราการผลิตเพิ่มขึ้นจำนวน 18%
Anheuser-Busch InBev เป็นผู้ผลิตที่มีการขยายกำลังการผลิตตามแนวโน้มการขยายตัวของตลาด โดยการขยายตลาดมีมากกว่า Budweiser และ Bud Light รวมไปถึงยี่ห้ออื่นๆ อีกกว่า 200 ยี่ห้อ
แต่การผลิตเบียร์เพื่อให้ได้ตามความต้องการที่หลากหลายเป็นเรื่องท้าทายอย่างมาก และบริษัทมองเห็นว่าข้อจำกัดของการผลิตอยู่ที่การผลิตในขั้นตอนท้ายๆอันเนื่องจากว่าต้องมีการหยุดการผลิตตามแผน (planned downtime) เช่น หยุดเพื่อการตั้งเครื่องให้ผลิตได้ตามแผน หรือ เปลี่ยนยี่ห้อตามแผนการผลิต ซึ่งการผลิตตามจำนวนยี่ห้อมากขึ้นเท่าไหร่จะยิ่งทำให้ต้องมีการหยุดการผลิต (downtime) จำนวนครั้งมากขึ้นตามไปด้วย
ทีมผู้ทำงานในโครงการ Lean Six Sigma เลือกใช้ Minitab เพื่อช่วยในการวิเคราะห์ข้อมูลซึ่งผลจากการวิเคราะห์ ไม่เพียงแต่ทำให้สามารถลดระยะเวลา downtime ลงได้แต่ยังหาวิธีช่วยลดต้นทุนลงอีกด้วย แต่วิธีการแก้ปัญหาที่เราได้มานั้นจะสามารถนำไปใช้กับทุกกรณีได้หรือไม่ นั่นเป็นสิ่งที่เราต้องหาคำตอบด้วยเช่นกัน
สิ่งท้าทาย
Anheuser-Busch InBev ต้องการทำให้เกิดการผลิตที่หลากหลายขึ้นโดยทำให้ประสิทธิภาพการผลิตดีขึ้น ด้วยการลดระยะเวลา downtime
ทีมผู้ทำงานมาจากหลายๆคนที่อยู่ในธุรกิจนี้ โดยมีการทำงานร่วมกันเพื่อกำหนดเป้าหมายของธุรกิจนำร่อง โดยเป้าหมายที่ตั้งไว้คือ ลดระยะเวลา downtime 30% และลดต้นทุนให้ได้ $200,000 รวมทั้งยังกำหนดประโยชน์เพิ่มเติมอื่นที่อาจจะเกิดขึ้นได้ เช่น ลดพลังงานในการผลิต และเพิ่มกิจกรรมที่ทำให้พนักงานมีความผูกพันกับองค์กรมากขึ้น (operator engagement)
บริษัทไม่ได้มีการวางรูปแบบในการลดระยะเวลา downtime อย่างเป็นทางการ รวมทั้งทีมงานยังต้องการที่จะสร้างชุดเครื่องมือที่จะสามารถนำไปช่วยในการทำซ้ำในบริษัทอื่นๆทั่วโลก และเพื่อให้แน่ใจว่าชุดเครื่องมือที่จะสร้างขึ้นมานี้จะมีประสิทธิภาพจริงๆ จึงได้มีการทำสำรวจกับพนักงานว่าชุดเครื่องมือที่สร้างขึ้นมานี้มีความง่ายในการเรียนรู้และใช้งานอย่างไร โดยคะแนนรวมที่ได้ควรจะอยู่ในช่วง 4.5 – 5 เป็นอย่างน้อย
Minitab มีส่วนช่วยอย่างไร
คุณจะสามารถแก้ปัญหาได้ก็ต่อเมื่อคุณเข้าใจปัญหานั้น ในการหาสาเหตุรากเหง้าของการเกิด downtime ทีมงานเริ่มต้นด้วยการเก็บข้อมูล โดยทำการร่างรายละเอียดของกระบวนการทำงานและเขียนแผนภาพการไหลของการทำงานของพนักงานแต่ละคน จากนั้นทำการเก็บค่าเวลาการทำงานและจำนวนของเสียที่เกิดขึ้นในการทำงานของแต่ละสายการผลิตและพนักงานแต่ละคน โดยทำการเก็บข้อมูลเวลาในการทำกิจกรรมของทุกกิจกรรมอย่างละเอียด เช่น การใส่ถุงมือ การหยิบจับเครื่องมือ จากนั้นจึงนำข้อมูลเหล่านั้นมาวิเคราะห์ด้วยเครื่องมือทางสถิตของ Minitab เช่น แผนภาพพาเรโตเพื่อดูว่าสิ่งใดที่ทำให้เกิด downtime มากที่สุดคืออะไร ส่วนฮีสโตแกรมทำให้เข้าใจพฤติกรรมของกระบวนการ และ แผนภูมิควบคุมและกราฟอื่นเพื่อใช้ในการเปรียบเทียบผลลัพธ์ที่ได้จากแต่ละโรงการผลิตและกะทำงานที่แตกต่างกัน
ทีมงานยังมีการใช้คำสั่ง Minitab’s Assistant เพื่อช่วยในการตัดสินใจว่าควรใช้วิธีการวิเคราะห์แบบใด และทำให้ผลลัพธ์ออกมาเป็นรายงานได้อย่างเหมาะสม รวมทั้งมีการใช้ ANOVA ในการเปรียบเทียบค่าเฉลี่ย การทดสอบสมมติฐานเพื่อดูว่าความแตกต่างนั้นมีนัยสำคัญหรือไม่ โดยความแตกต่างระหว่างกะทำงานนั้นมีผลต่อการทำงานกระบวนการอย่างมีนัยสำคัญ
ทีมงานยังใช้ Minitab’s boxplots และกราฟอื่นๆเพื่อทำให้เห็นว่ากะทำงานที่แตกต่างกันนั้นให้ผลลัพธ์ของการผลิตยี่ห้อที่แตกตต่างกันมีความแตกต่างกัน
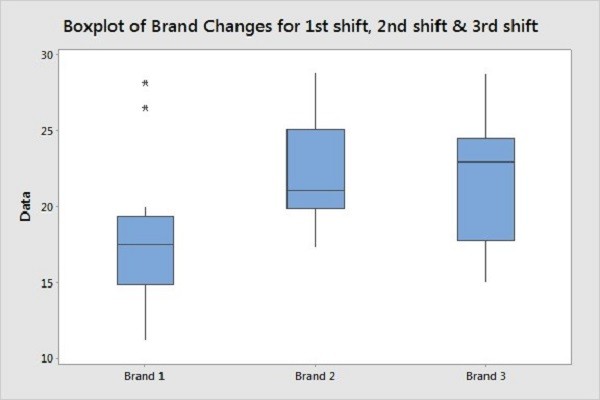
ในการวิเคราะห์หาสาเหตุรากเหง้าของความแตกต่างนี้ ทางทีมงานมีการใช้การวิเคราะห์ระบบการวัดในเรื่อง Gage R&R เพื่อทวนสอบว่าค่าการวัดนั้นมีความน่าเชื่อถือได้หรือไม่ก่อนที่จะมีการปรับปรุง ซึ่งในการวิเคราะห์พบว่า ไดอัลอินดิเคเตอร์ (dial indicator: นาฬิการวัด) และ ระยะเวลาการทำงานของกระบวนการ มีความไม่น่าเชื่อถือและควรจะต้องจัดการแก้ไขให้ดีเสียก่อน
เพราะความสามารถของการวิเคราะห์ของ Minitab ทำให้ทีมงานสามารถระบุได้ว่าสาเหตุที่แท้จริงของ Downtime ที่มีค่ามากกว่าความเป็นจริง นั้นมาจากขั้นตอนการปฏิบัติงานในการเปลี่ยนสายการผลิตนั้นมีความไม่เหมาะสม และสาเหตุที่ทำให้เกิดความแตกต่างอย่างมีนัยสำคัญคือ กะเวลาทำงานที่แตกต่างกันทำให้เกิดความแตกต่างกัน รวมถึงสิ่งอำนวยความสะดวกและกระบวนการที่แตกต่างกันด้วย
ต่อไปเป็นการวิเคราะห์เพื่อดูว่าวิธีการแก้ปัญหาที่พบนี้จะสามารถนำไปใช้ได้ทั่วโลกหรือไม่ โดยทำการหาวิธีการปรับเปลี่ยนกระบวนการที่ควรจะเป็น โดยทีมงานเริ่มจากการระดมสมองเพื่อรวบรวมความคิด และค้นหาสาเหตุรากเหง้ารวมทั้งเรียงลำดับถึงผลกระทบและความยากง่ายในการแก้ไข เมื่อได้ความคิดทั้งหมดจะนำมาเรียงลำดับตามโรงงานผลิตและกระบวนการผลิตเพื่อเป็นการทวนสอบความแตกต่างทั้งหมดไปพร้อมๆกันด้วย ในรายการวิธีแก้ปัญหาที่ค้นพบ ได้แก่ วิธีการเปลี่ยนกระบวนการผลิตที่เหมาะสมด้วยการทำให้เกิดการทำงานอัตโนมัติเพื่อทำให้เกิดสายการผลิตที่มีประสิทธิภาพ ซึ่งทำให้เวลา downtime ลดลง จากที่ต้องมีการทำงานตามขั้นตอน 30 หน้าเหลือเพียงขั้นตอนการทำงานตาม check list จำนวน 1 หน้าเท่านั้น ทีมงานยังได้วางแผนจะทำการฝึกอบรมให้กับพนักงานในสายการผลิตเพื่อให้สามารถทำงานได้เป็นมาตรฐาน และเพิ่มตัวจับเวลาแบบ LED ในสายการผลิตเพื่อทำให้เกิดการส่งข้อมูลค่า downtime ที่ถูกต้องขึ้น รวมถึงทำให้เกิดความตระหนักรู้ว่าความเร่งด่วนคืออะไร
ในการทวนสอบว่าวิธีการแก้ปัญหานี้ ทีมงานได้มีการสร้างแผนที่มีการลงรายละเอียดที่ใช้กับกระบวนการผลิตต้นแบบและดูว่าผลกระทบที่เกิดขึ้นนั้นเป็นอย่างไรเมื่อเปรียบเทียบกับเป้าหมายที่ตั้งไว้ตั้งแต่ต้น และในระยะของการเตรียมพร้อมสำหรับการนำไปใช้งาน สิ่งที่เห็นได้ชัดเจนว่ามีการเปลี่ยนแปลง คือ ความมีส่วนร่วมของพนักงานในการทำงาน พนักงานที่ทำงานในกะทำงานที่แตกต่างกันต่างตื่นเต้นที่จะดูความเปลี่ยนแปลงที่จะเกิดขึ้นและเตรียมพร้อมที่จะแข่งขันกันให้ได้ผลลัพธ์ที่ดีขึ้น
ผลของการศึกษา
เมื่อทดลองนำไปใช้งานพบว่าวิธีการทำงานที่ปรับปรุงนั้นทำได้ดีกว่าที่คาดหวังไว้มาก โดยผลของการปรับปรุงคือ ลดเวลา downtime ได้ 34% และลดต้นทุนลงได้กว่า $430,000 เมื่อเวลา downtime ลดลงเท่ากับว่าการเปลี่ยนกระบวนการผลิตจะใช้ทรัพยากรลดลงและทำให้ประหยัดมากขึ้น
ทีมงานยังพบอีกว่าการปรับปรุงนี้ทำให้การผลิตสามารถกลับมาผลิตได้เร็วขึ้นเกือบ 40% ซึ่งเท่ากับเน้นย้ำว่าการปรับปรุงครั้งนี้ทำให้ได้ประโยชน์เพิ่มขึ้น จากแผนภูมิควบคุมที่ Minitab สร้างขึ้น เป็นการยืนยันผลการเปลี่ยนแปลงเชิงบวกที่เกิดขึ้น รวมทั้งยังนำค่าของเส้นควบคุมไปเป็นตัวทวนสอบกระบวนการเพื่อดูว่ากระบวนการยังสามารถทำงานได้ตามความสามารถนี้ตลอดเวลา
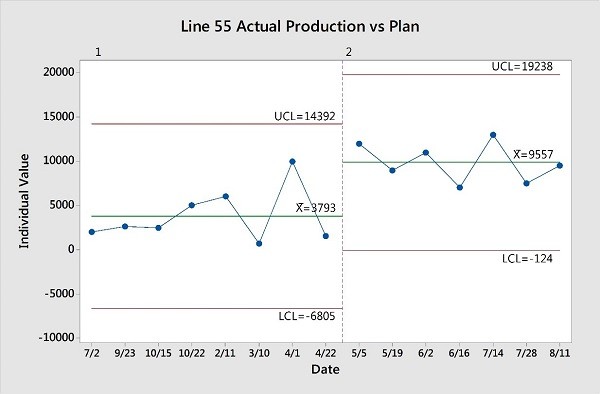
แผนภูมิควบคุมที่ Minitab สร้างขึ้นจะถูกนำไปใช้เพื่อยืนยันว่าผลลัพธ์ที่ได้นี้จะคงอยู่ต่อไปในอนาคต
การเปลี่ยนแปลงที่ทีมงานทำนั้น สามารถนำไปรวมเป็นชุดเครื่องมือซึ่งสามารถนำไปใช้กับกระบวนการอื่นๆได้ พนักงานมีความพึงพอใจในวิธีการทำงานตาม checklist ที่ได้รับการคิดค้นมาว่ามีส่วนช่วยลดเวลาในการทำงาน และให้ผลการประเมินประสิทธิภาพของชุดเครื่องมือนี้ด้วยคะแนน 4.8 (เต็ม 5) ทั้งนี้ผลการสำรวจยังระบุว่าพนักงานให้ความร่วมมือในการทำงานของพวกเขามากขึ้น โดยเฉพาะเมื่อรู้ว่างานที่พวกเขาทำนั้นทำให้เกิดความเปลี่ยนแปลงขึ้น
ผลลัพธ์เหล่านี้ทำให้ทีมงานมีความมั่นใจว่าพวกเขาสามารถนำชุดเครื่องมือนี้ไปใช้งานได้อย่างแพร่หลายและมีประสิทธิภาพ ชุดเครื่องมือได้ถูกนำไปใช้กับกระบวนการนับหมื่นที่มากกว่า 180 แห่งทั่วโลก และสร้างความสำเร็จอย่างชัดเจน
การรวบรวมข้อมูลของ downtime ของกระบวนการและวิเคราะห์ด้วย Minitab นั้นทำให้เกิดผลลัพธ์ที่ส่งผลต่อความสามารถของ Anheuser-Busch InBev ในการผลิตเบียร์ ให้สามารถตอบสนองต่อความหลากหลายตามความต้องการของลูกค้า และนั่นคือความสำเร็จในคุณภาพและประสิทธิภาพที่ทุกคนยกย่องชื่นชม
กรณีศึกษานี้อ้างอิงมาจาก การนำเสนอผลงานของ Anheuser-Busch InBev ในงาน ASQ’s 2014 International Team Excellence Award ไฟล์การนำเสนอนี้มีให้สำหรับสมาชิก ASQ และการลงทะเบียนไม่เสียค่าใช้จ่ายได้ที่ Download the Anheuser-Busch InBev presentation.
บทความต้นฉบับ : Anheuser-Busch InBev meets customer demand by streamlining production
ต้นฉบับนำมาจาก Minitab Case Study , แปลและเรียบเรียงโดยสุวดี นำพาเจริญ,
บริหารจัดการ SCM Blog โดยชลทิชา จำรัสพร บริษัท โซลูชั่น เซ็นเตอร์ จํากัด ตัวแทน Minitab ในประเทศไทย

เพิ่มเติมเกี่ยวกับบริษัท Minitab
Minitab ช่วยให้บริษัทและองค์กรต่างๆ สามารถมองเห็นแนวโน้มของข้อมูล, แก้ปัญหาและค้นพบประเด็นสำคัญจากข้อมูลเชิงลึก โดยนำเสนอชุดโซลูชั่นที่ครอบคลุมทุกด้านและดีที่สุดสำหรับซอฟต์แวร์ในระดับเดียวกัน ที่ใช้สำหรับการวิเคราะห์ข้อมูลและการปรับปรุงกระบวนการ
ด้วยวิธีการที่เป็นเอกลักษณ์ และการนำเสนอซอฟต์แวร์และบริการแบบองค์รวม Minitab ช่วยให้องค์กรเข้าถึงกระบวนการตัดสินใจในส่วนที่ช่วยผลักดันให้เกิดความเป็นเลิศทางธุรกิจได้ดีขึ้น ความง่ายในการใช้งานที่โดดเด่นกว่าใครมีส่วนช่วยให้ Minitab สามารถทำให้การเข้าถึงข้อมูลเชิงลึกเป็นเรื่องที่ง่าย ทีมงานของ Minitab ซึ่งประกอบด้วยผู้เชี่ยวชาญทางด้านการวิเคราะห์ข้อมูลที่ได้ผ่านการอบรมมาเป็นอย่างเข้มงวด จะช่วยให้ผู้ใช้งานมั่นใจว่าจะได้รับประโยชน์สูงสุดจากการใช้งานวิเคราะห์ข้อมูลและพร้อมที่จะให้คำปรึกษาตลอดเวลาที่ใช้งานเพื่อนำไปสู่การตัดสินใจที่ดีขึ้น รวดเร็ว และแม่นยำ
เป็นเวลากว่า 50 ปีที่ Minitab ได้ช่วยองค์การต่าง ๆ เพิ่มรายได้ ควบคุมและลดต้นทุน เพิ่มคุณภาพ เสริมสร้างความพึงพอใจของลูกค้า และเพิ่มประสิทธิภาพ ธุรกิจและองค์นับหมื่นทั่วโลกใช้ Minitab Statistical Software®, Companion by Minitab®, Minitab Workspace®, Salford Predictive Modeler® and Quality Trainer® เป็นเครื่องมือช่วยในการค้นพบและปรับปรุงความบกพร่องในกระบวนการ